Gas vs. Gasless MIG Welders: Which Is Right for You?
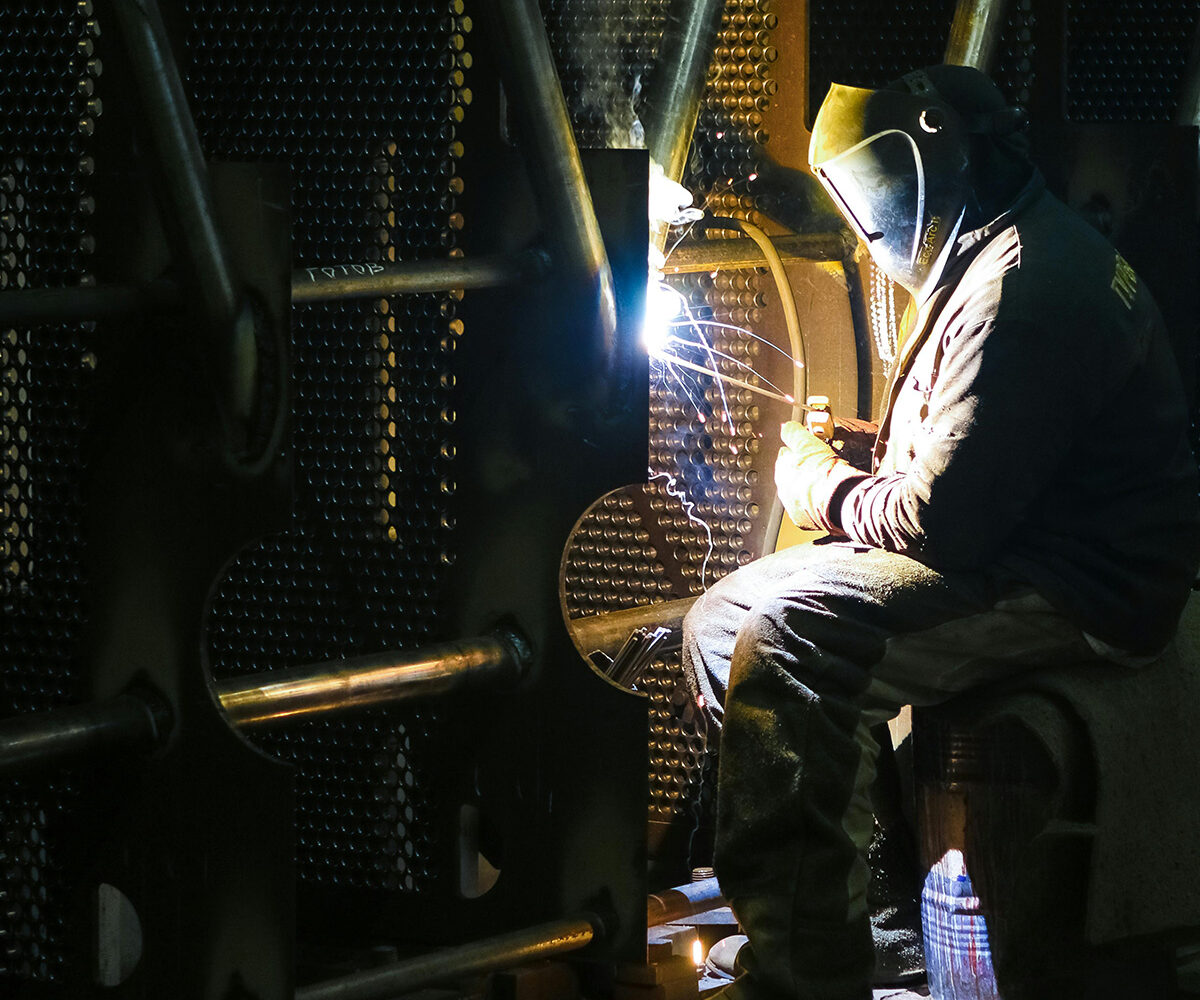
MIG welding, short for Metal Inert Gas welding, is a popular and versatile method for various welding applications. When selecting a MIG welder, one crucial decision is choosing between gas and gasless models. Understanding the differences between gas vs. gasless MIG welders can significantly impact your welding projects. This guide will help you navigate these options to find the best fit for your needs.
Understanding the Basics between a Gas and Gasless MIG Welder
Gas MIG Welding
Gas MIG welding, often called MIG welding, uses a shielding gas—typically argon or a mix of argon and carbon dioxide—to protect the weld from atmospheric contamination. The gas helps produce cleaner, higher-quality welds with minimal spatter. This method is highly effective for welding thin materials and is commonly used in professional settings.
Gasless (Flux-Core) MIG Welding
Gasless MIG or flux-core welding employs a flux-cored wire instead of an external shielding gas. The flux inside the wire generates a protective gas shield as it melts, making it suitable for outdoor welding or windy conditions where gas shielding would be disrupted. This method is often used for heavier materials and is favoured for its portability and ease of use.
The main differences between a Gas and Gasless MIG Welder
Aspect | Gas MIG Welder | Gasless MIG Welder |
Shielding Method | Uses external gas (argon or gas mix) | It uses flux-cored wire that generates its shielding gas |
Weld Quality | Cleaner welds with minimal spatter | More spatter and rougher finish |
Portability | Less portable due to gas cylinders | More portable; no need for gas cylinders |
Outdoor Use | Not ideal for windy or outdoor conditions | Suitable for outdoor use and windy conditions |
Cost | Higher initial cost due to gas equipment | Lower initial cost; no gas cylinders required |
Pros and Cons of Gas MIG Welders
Advantages
- Cleaner Welds: Gas MIG welders produce smooth and clean welds with minimal spatter, producing a more professional finish.
- Better for Thin Materials: Gas MIG welding offers precise control, ideal for welding thin metals without burning through.
- Professional Quality: These welders are often used in industrial and high-quality applications due to their superior performance.
Disadvantages
- Requires Gas Cylinders: Gas MIG welding necessitates using gas cylinders, which can be cumbersome and add to the overall cost.
- Less Portable: The need to transport and manage gas cylinders makes gas MIG welders less portable than gasless models.
- More Expensive: The initial setup cost, including the gas cylinders and associated equipment, can be higher.
Pros and Cons of Gasless MIG Welders
Advantages
- More Portable: Gasless MIG welders are more portable as they don’t require gas cylinders, making them easier to move and use in various locations.
- Cheaper: Gasless welders generally have a lower initial cost, making them a budget-friendly option for hobbyists and occasional users.
- Good for Outdoor Use: The self-shielding flux makes these welders effective in outdoor or windy environments.
Disadvantages
- More Spatter: Gasless MIG welding can produce more spatter and a rougher finish than gas MIG welding.
- Lower Quality Welds: The welds might need to be cleaner or more aesthetically pleasing, and the quality can vary depending on the material and settings.
- Limited to Thicker Materials: Gasless MIG welders are typically better suited for thicker materials and may not provide the finesse for thin metals.
Which Welder Should You Choose?
When deciding between gas and gasless MIG welders, consider the following factors:
- Project Type: A gas MIG welder is generally preferred for delicate, precise work on thin materials. A gasless MIG welder might suit larger, thicker projects or outdoor work.
- Budget: If you’re on a tight budget, gasless MIG welders offer a more affordable entry point. However, if you’re looking for high-quality welds and are willing to invest more, a gas MIG welder may be worth the extra cost.
- Location: Gas MIG welders are ideal for indoor environments where gas shielding can be maintained. Gasless welders excel in outdoor settings or situations where portability is key.
Conclusion
In choosing between gas and gasless MIG Welders, it’s essential to weigh the key differences and how they align with your specific needs. Gas MIG welders offer cleaner welds, are ideal for thin materials, and are often preferred for high-quality, professional work. However, they require gas cylinders, are less portable, and have a higher initial cost. On the other hand, gasless MIG welders provide greater portability and lower costs. They are suitable for outdoor or windy conditions but may produce more spatter, offer lower weld quality, and are better suited for thicker materials.
- Choose a gas MIG Welder if you prioritise a clean, professional finish, work primarily indoors, and are willing to invest in higher initial costs for superior performance.
- Opt for a gasless MIG Welder if you need a budget-friendly, portable, effective option in outdoor settings, working with thicker materials, or requiring a more flexible setup.
Toolden’s Best Sellers
Sealey MIGHTYMIG170 Professional Gas/No-Gas MIG Welder 170Amp with Euro Torch
- 170A Maximum Performance: Delivers powerful welding capability for professional use.
- Gas/No-Gas Versatility: It is ready to use in gas mode and easily switchable to gasless by changing polarity.
- Ergo 15.2 Euro Torch: High-quality, cool-running torch for extended use.
- Complete Accessories: This includes a 2m earth cable, 1.4m gas hose, twin-gauge gas regulator, and 0.6mm and 0.8mm contact tips.
- Gas Bottle Compatibility: Shown for size reference (gas bottle not included).
- Durable Construction: Built for professional performance at an affordable price.
SIP 05740 WELDMATE AUTOPLUS 200A MIG/ARC/TIG Welder 230V
- Multi-process MIG/ARC/TIG welder for greater flexibility.
- Pure Synergic Control for more consistent and higher quality welds.
- Fully compliant with EU 2019/1784 (Eco Design for Welding Equipment).
- Heavy-duty aluminium wire feeder for a smooth, consistent flow of wire.
- An intuitive control panel selects between process, gas, and wire size.
- Metal casing with strong-grip carry handle for long-life use.
Parweld XTM256i 250A MIG Inverter Package 400V
- Multi-process capability: MIG, TIG, and MMA welding
- Operates on 400V three-phase power
- Easy selection of welding processes, control type, material, and wire size
- Synergic control for automatic parameter adjustment
- Fan on demand for efficient cooling
- 2T / 4T trigger latching for versatile operation
- Real-time display of parameters and data
- Soft switching technology for improved efficiency
- Clear visor to protect front panel controls
- Supplied with gas hose and 3m earth lead
FAQ
What safety gear should I wear when using a MIG Welder?
Always wear a welding helmet with the appropriate lens shade to protect your eyes and face from bright sparks and UV radiation. Use flame-resistant gloves, long-sleeve welding jackets, and safety boots. Additionally, wear hearing protection and a welding apron if needed.
How should I handle and store gas cylinders safely?
- Handling: Always secure gas cylinders upright and use appropriate regulators and hoses. Avoid dropping or mishandling cylinders.
- Storage: Store gas cylinders in a well-ventilated area away from flammable materials and direct sunlight. Ensure they are properly secured to prevent tipping.
How can I manage welding fumes and ventilation?
Always weld in a well-ventilated area or use a welding fume extraction system to avoid inhaling harmful fumes and gases. If welding indoors, ensure adequate ventilation to disperse fumes.
At Toolden, we offer various Mig Werlders for domestic and commercial applications.
Need help deciding which to choose? Need some help with your order? Our new help centre has a wide range of helpful articles and guides!
If you have any additional queries, please do not hesitate to contact us at 01358 726719 or by email at admin@toolden.co.uk