Top 5 Mistakes to Avoid When Using a Torque Wrench

A torque wrench is an indispensable tool for ensuring the precise tightening of bolts and fasteners, which is crucial in fields like automotive repair, machinery maintenance, and construction. It prevents under-tightening, which can lead to loose fasteners, and over-tightening, which can damage parts. While the tool is easy to use, common pitfalls can compromise its effectiveness and lead to disastrous outcomes, from stripped threads to component failure.
In this expanded blog post, we’ll explore the top five mistakes to avoid when using a torque wrench and how to ensure the accuracy, safety, and longevity of your tool and your project.
Why are branded tools important?
Branded tools are essential because they offer superior quality, reliability, and durability. Leading brands are known for using high-grade materials and adhering to strict manufacturing standards, ensuring their tools perform consistently over time. Additionally, branded tools often come with warranties and dedicated customer support, providing users with peace of mind and protection against defects or malfunctions. These brands also prioritise innovation, integrating the latest technology, safety features, and ergonomic designs to improve efficiency and user experience. Investing in branded tools is a smart choice for long-term performance and reliability.
Top 5 Mistakes to Avoid
Over-Tightening Fixings
Over-tightening fixings is a common mistake, especially when users believe “tighter is better.” However, excessive force can distort or crush components, particularly those of softer metals or delicate materials. In worst-case scenarios, it could lead to shearing off bolts entirely or causing the fastener to fail prematurely.
Common Causes
- Not trusting the torque wrench’s indication (the “click”).
- Lack of proper torque specification knowledge.
- Using a regular wrench instead of a torque wrench, applying too much force.
How to Avoid it
- Always refer to the manufacturer’s recommended torque specifications and trust your torque wrench once it indicates the target torque has been reached.
- Make sure the wrench is calibrated to provide accurate results.
- Avoid the temptation to “just give it one more turn,” which can cause unnecessary damage.
Pro Tip: Be careful when handling sensitive components like spark plugs or aluminium parts, as excess force can easily damage these materials.
Damaging Threads
Damaged threads can result from overtightening, cross-threading, or using the wrong tools. They affect the integrity of the bolt and the component it’s being fastened to, leading to weakened connections or, in extreme cases, a total failure of the fastening system.
Common Causes
- Cross-threading when installing bolts.
- Over-tightening leads to thread stripping.
- Not using thread lubricants where specified.
How to Avoid It
- Always ensure the bolt is properly aligned before beginning to tighten. If it feels binding, back it out and start again to avoid cross-threading.
- Avoid excessive force that can strip or stretch the threads.
- Fasteners in high-friction areas should use appropriate lubricants to reduce the risk of thread damage.
Pro Tip: For high-stress components, consider using thread-locking compounds to prevent loosening, but avoid using them to compensate for damaged threads.
Using Mismatched Sockets
Using the wrong socket size can damage the fastener head, rounding off the bolt or nut. This makes future removal difficult and can compromise the torque applied, leading to under- or over-tightening, compromising the fastening job.
Common Causes
- Grabbing a socket that “almost fits” rather than finding the exact size.
- Using worn or cheap sockets that don’t grip properly.
- Mixing metric and imperial tools, which are often close but different.
How to Avoid it
- Always use the correct size socket that fits snugly on the bolt or nut head. Avoid sockets that feel loose or require extra force to fit.
- Invest in high-quality sockets that maintain a good grip even after long-term use.
- Double-check whether you need metric (mm) or imperial (inch) sizes, especially when working with mixed systems. While using a 13mm socket on a 1/2-inch fastener (12.7mm) might seem to work, it’s not precise and can damage the fastener.
Pro Tip: If you frequently work with metric and imperial fasteners, consider keeping a dual-socket set to avoid using near-size alternatives that can damage fasteners.
Purchasing the Wrong Wrench Size
Torque wrenches come in various sizes, typically from small 1/4-inch drives to larger 3/4-inch or even 1-inch drives. Choosing the wrong size wrench for the job can lead to inaccurate torque application, either because it doesn’t cover the torque range you need or because it’s too large or small for the fasteners you’re working with.
Common Causes
- Not understanding the torque range required for your project.
- Purchasing one wrench size and expecting it to cover all tasks.
- Using an improperly sized wrench for large or small fasteners.
How to Avoid It
- Ensure you choose a wrench that can handle the torque range needed for your project. A 1/4-inch or 3/8-inch drive wrench is ideal for smaller bolts, while larger fasteners require a 1/2-inch or 3/4-inch drive.
- Don’t assume a single wrench will cover everything—it’s better to have two or more torque wrenches to cover the full range of fasteners you commonly use.
- Use the right torque wrench size for the job. Avoid using a large wrench for delicate, small fasteners and vice versa, as this can lead to inaccuracy.
Pro Tip: When purchasing a torque wrench, consider its range’s minimum and maximum torque values. If you work on various tasks, it might be worth investing in more than one wrench to accurately handle both low and high-torque applications.
Using the Wrong Torque Setting
Every bolt or fastener has a specific torque requirement, usually provided by the equipment manufacturer. Tightening a fastener too loosely could result in vibrations loosening the bolt over time, potentially causing a dangerous failure. Conversely, over-tightening can stretch or break the bolt, damage the threads, or crack the material the fastener is holding together.
Common Causes
- Misreading the manual or spec sheet.
- Confusing units of measurement (Nm vs ft-lb).
- Relying on memory rather than checking specifications.
How to Avoid It
- Always verify the torque specification for the fastener you’re working with. This information is usually in the equipment’s user manual or repair guide.
- Use the correct unit of measure. Torque wrenches can be calibrated in Newton meters (Nm), foot-pounds (ft-lb), or inch-pounds (in-lb). Ensure that your wrench is set to the same unit provided in the specification.
- Double-check the adjustment scale on the wrench to ensure the right torque level has been set. Don’t rely on estimation or memory.
Pro Tip: If you regularly work with metric and imperial systems, consider owning two torque wrenches, each calibrated for a specific unit (Nm and ft-lb), to avoid confusion and the risk of miscalibration.
Best Sellers
Teng Tools 1292AG-EP Torque Wrench 40-210nm 1/2″ Drive
- Torque wrench, according to DIN3122
- The ratchet torque wrench can tighten and final check the torque.
- Reversible with lever, but only for right-hand action for torque checking
- Equipped with angular gauge for after tightening graduated in Nm and ft lb
- Lockable setting and accuracy : +/- 4%
- Satin finish
- Rubber handle
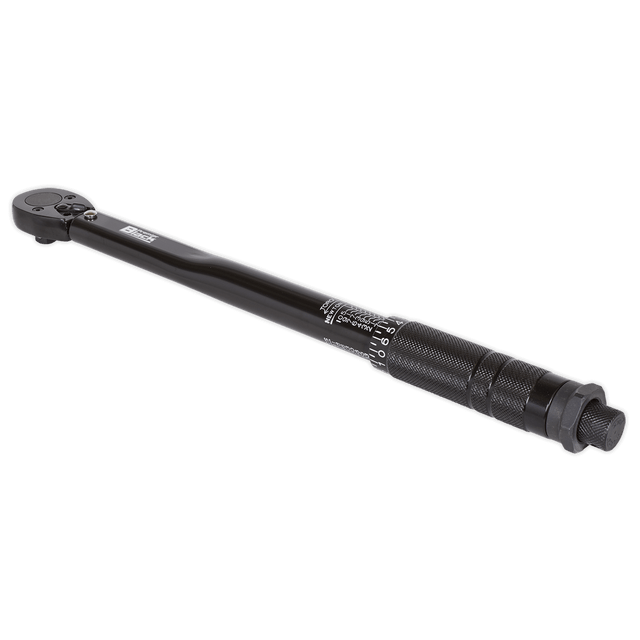
Sealey AK623B 3/8″Sq Drive Calibrated Micrometre Torque Wrench – Black Series
- Heat-treated steel ratchet head
- Fully hardened and tempered
- Electrodeposition finish for corrosion resistance
- Calibration tolerance by BS EN ISO 6789-1:2017
- Range: 7-112Nm(5-83lb-ft)
- Every wrench is tested and supplied with an individually numbered test certificate.
- Micrometre-type torque range adjustment with a scale graduated in both lb-ft and Nm.
- Flip reverse ratchet mechanism
Sealey STW900SET Torque Wrench Micrometre Style 3pc Set
- One of a comprehensive range of Premier Hand Tools, suitable for daily professional use.
- Flip reverse Chrome Vanadium steel ratchet head with a smooth action mechanism.
- Scales graduated in both Nm and lb. ft.
- Calibration tolerance by BS EN ISO 6789-1:2017.
- Wrenches are individually tested to standards with ±4% accuracy, and each wrench is issued with an individually numbered test certificate.
- Aluminium knurled handle for comfort and control.
FAQ
Why is torque important?
Proper torque is crucial to ensure that bolts are fastened securely without being overtightened, which could cause them to stretch, damage threads, or compromise the assembly’s structural integrity.
Can I use my torque wrench as a regular wrench?
No, torque wrenches are specialised tools meant for precise applications. Using them like a regular wrench could lead to wear and inaccurate torque readings. Use standard wrenches for general fastening or loosening.
What is the best way to store a torque wrench?
- Always store it in its protective case.
- Keep it at its lowest setting (for click-type wrenches).
- Avoid areas with extreme temperatures or humidity.
- Never store it with tension in the spring, as this can lead to inaccurate readings.
What Are the Common Torque Wrench Sizes?
Common drive sizes for torque wrenches include:
- 1/4″ drive (low-torque applications)
- 3/8″ drive (medium-torque, e.g., motorcycles)
- 1/2″ drive (higher-torque, e.g., automotive)
- 3/4″ drive (heavy-duty applications)
Need help deciding which to choose? Need some help with your order? Our new help centre has a wide range of helpful articles and guides!
If you have any additional queries, please do not hesitate to contact us at 01358 726719 or by email at admin@toolden.co.uk